Project R.A.C.E.
No âmbito do “Project R.A.C.E.” (Reaction Application for Composite Evolution – Aplicação de Reação para a Evolução de Compósitos), a Hennecke, em colaboração com os principais parceiros da indústria, deu um passo de desenvolvimento decisivo que permite que complexos componentes ocos de compostos de fibra sejam agora fabricados em questões de segundos. Uma cadeia de processos para a produção de um suporte de placa de licença para motocicletas feito de material compósito de fibra de carbono em uma estrutura oca é o foco principal do projeto. Na construção convencional, o suporte de placa de licença pesa mais de 765 gramas. Como parte do Project R.A.C.E. o componente tem um peso total de apenas 265 gramas com desempenho aumentado. Isto representa uma economia de peso de mais de 60 por cento!
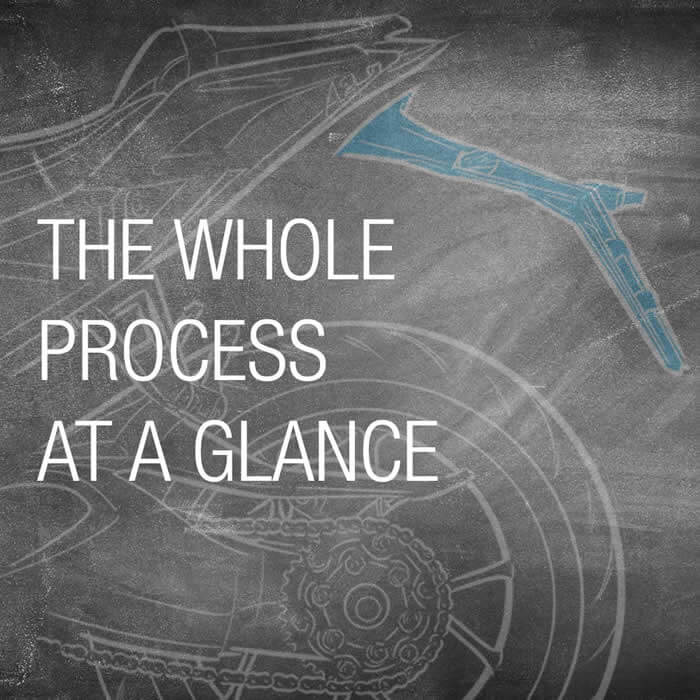
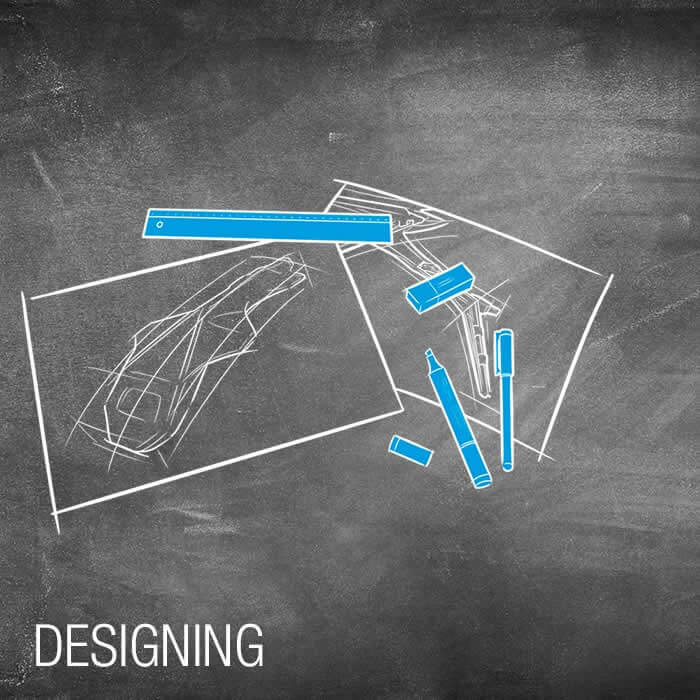
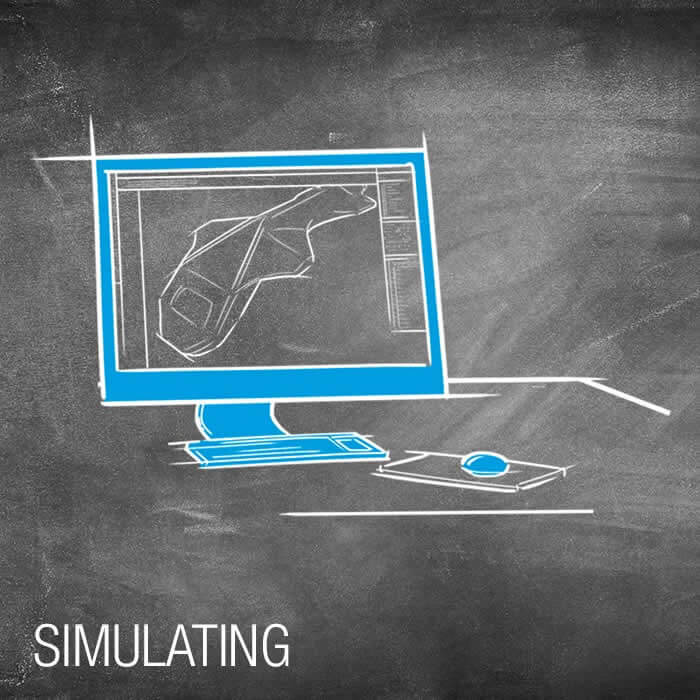
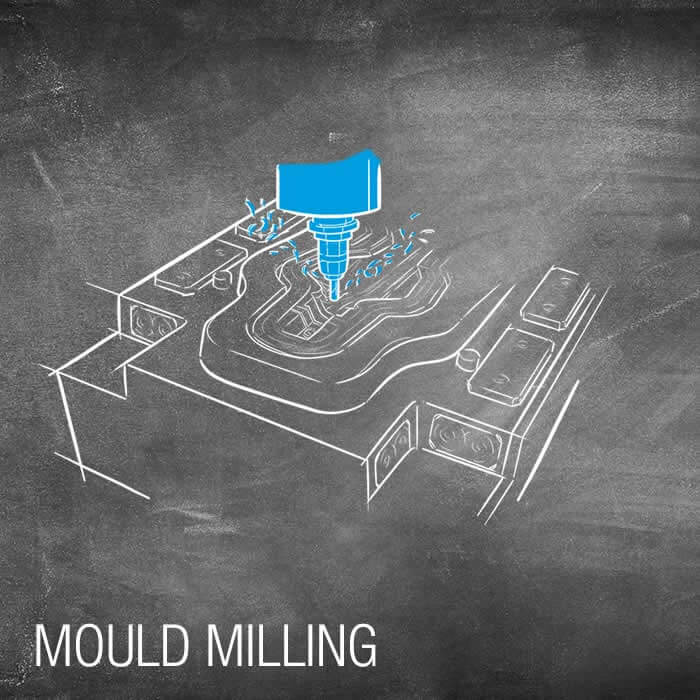
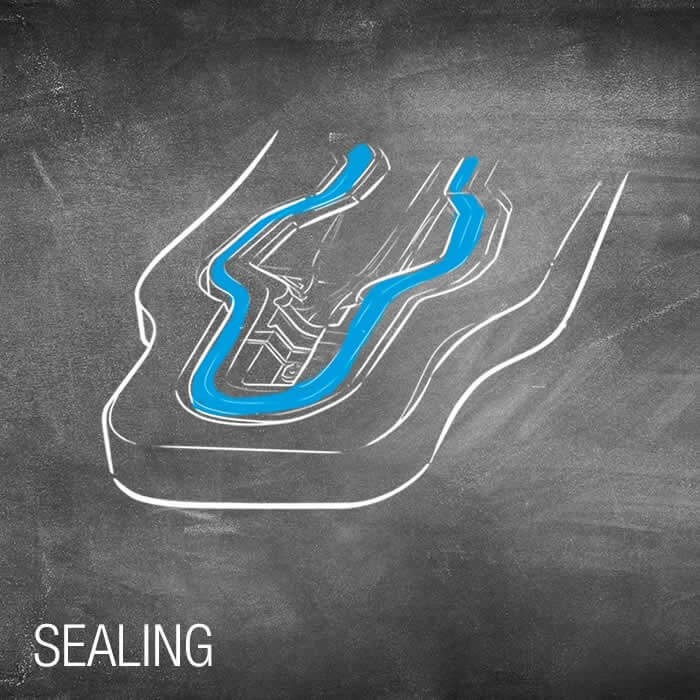
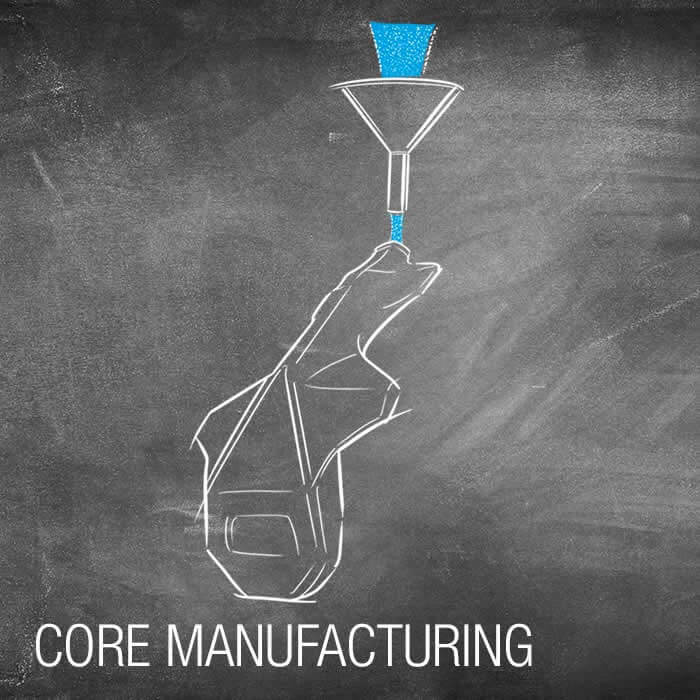
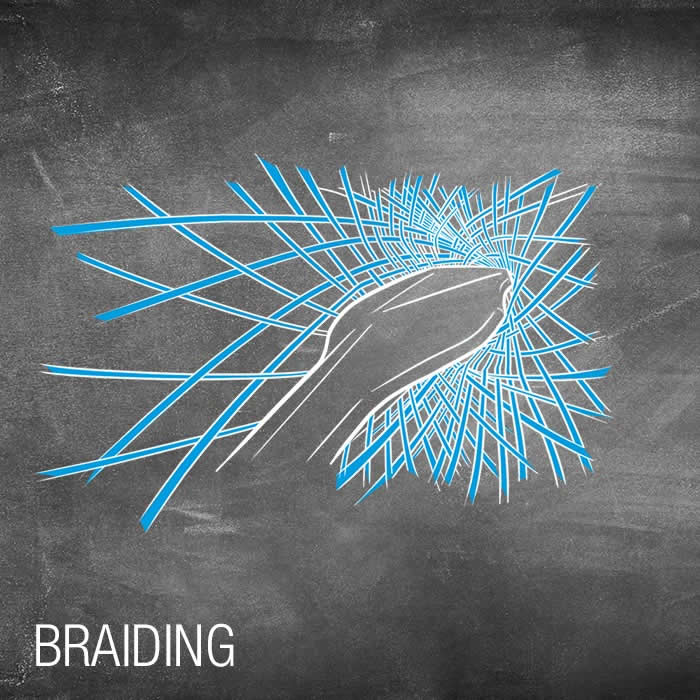
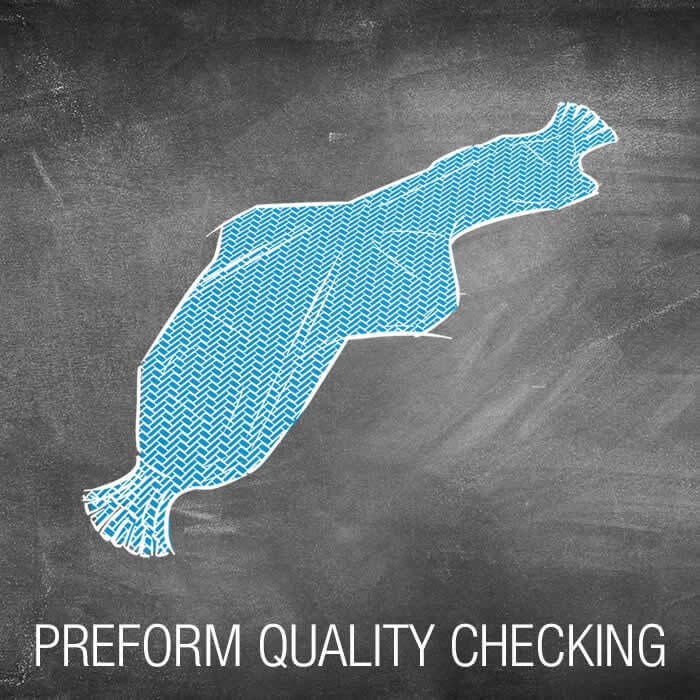
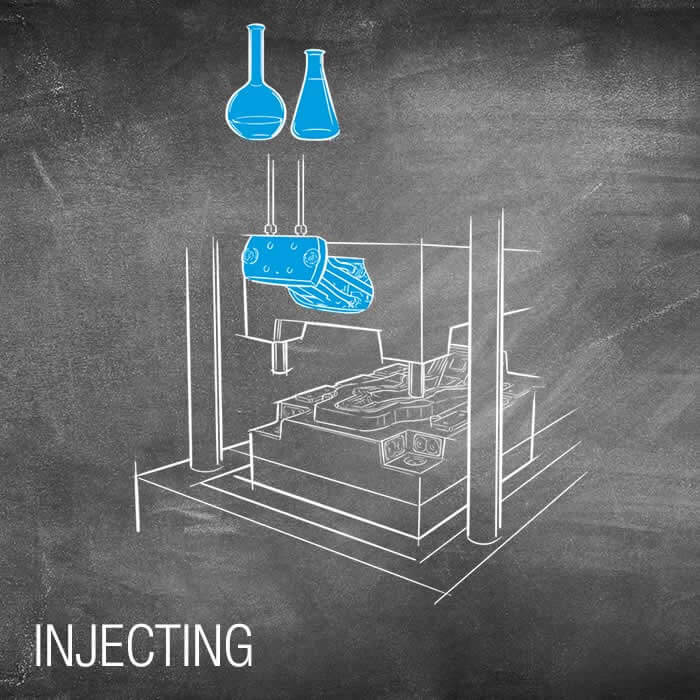
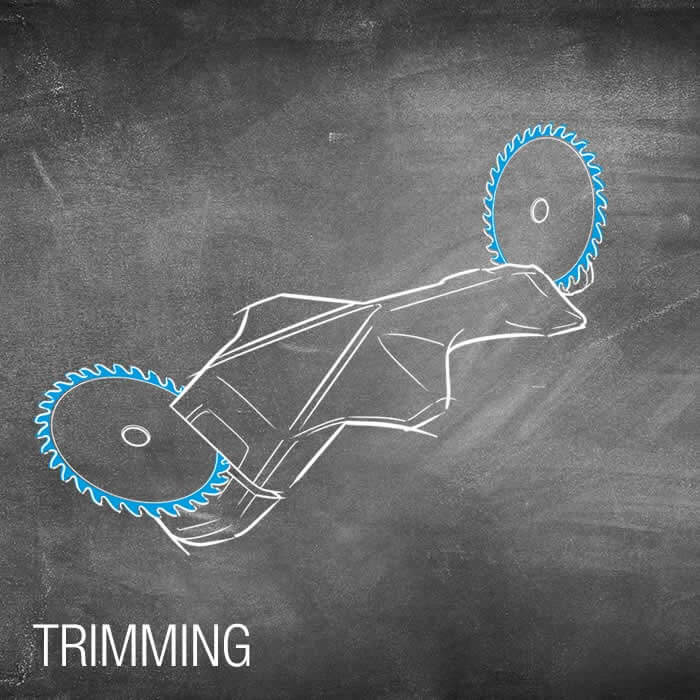
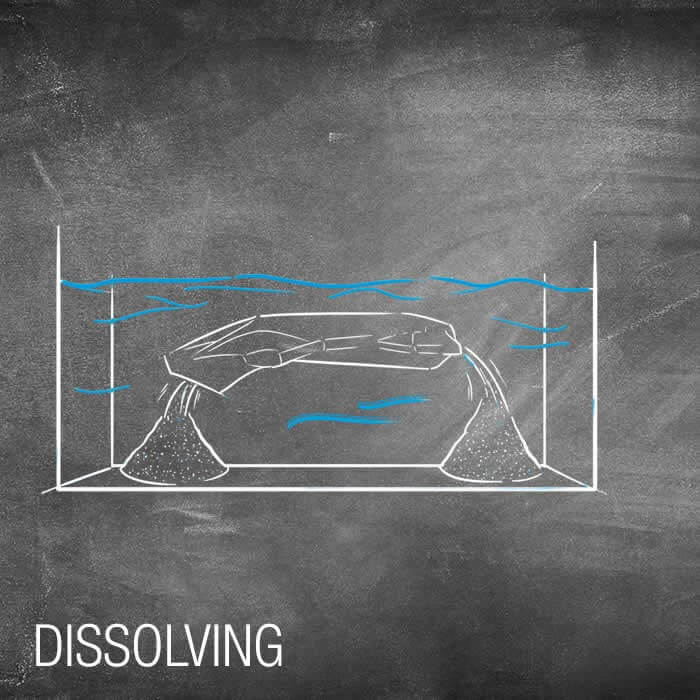
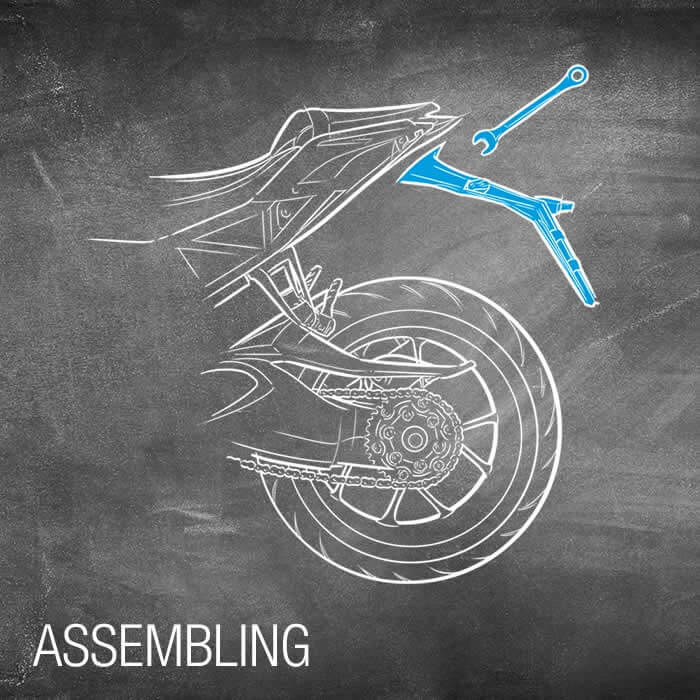
8 parceiros, 21 especialistas, 28 semanas de período de desenvolvimento
As condições gerais do Project R.A.C.E. foram claramente definidas
Sob a direção de Hennecke, o Project R.A.C.E. teve início com o objetivo de introduzir a nova tecnologia de produção CAVUS na produção em série. Em colaboração com os parceiros Engel, Huntsman, Murtfeldt, IFB Stuttgart, Persico, Reinsicht (anteriormente H2K Minerals) e KTM Technologies, foi formada uma equipe de trabalho holística internacional de 21 especialistas, que conferiram a si a missão de desenvolver um componente, desde ideias postas em uma folha de papel branca até a produção em série: O suporte de placa de licença para a KTM 1290 Superduke R. O desafio para este componente de alto desempenho reside na interação da concepção certa emparelhada com um design orientado para a produção e a combinação de processos eficientes baseados na inovadora tecnologia CAVUS da KTM Technologies. CAVUS designa a cadeia de processos automatizada para a produção de componentes ocos estruturais e complexos: Desde a fabricação do núcleo e a produção de pré-formas com fibras de carbono, por exemplo, na tecnologia de entrelaçamento, passando pelo processo HP-RTM até a desmoldagem do material do núcleo. Como resultado, podem ser alcançadas opções de configuração completamente novas em design e função.
A interação de design e engenharia constitui a base para um componente bem sucedido. Designers da Kiska e especialistas da KTM Technologies usam a abordagem "Inside Out Design" para o suporte de placa de licença da Superduke. Os primeiros desenhos a mão em papel formam a base para o processo de desenvolvimento, que inicia paralelamente. Aspectos como o espaço de montagem, conceito de conexão e a viabilidade de fabricação do componente são levados em consideração desde o início.
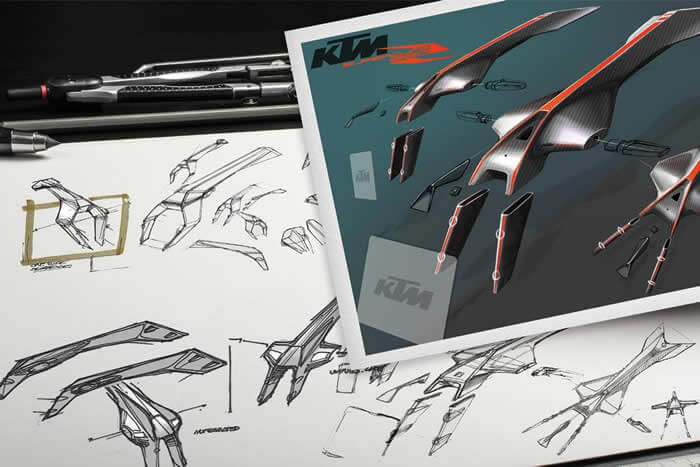
Para garantir a capacidade do processo desde a fase inicial do projeto, os engenheiros da IFB (Institut für Flugzeugbau – Instituto para Construção Aeronáutica) da Universidade de Stuttgart usam uma variedade de ferramentas de simulação. Após a transferência dos primeiros esboços para o software CAD, são feitas simulações estruturais do componente que fornecem uma estimativa inicial do número necessário de operações de entrelaçamento. Estes resultados serão utilizados no próximo passo para a simulação de entrelaçamento, que fornece informações sobre os ângulos de fibra resultantes e as possíveis áreas problemáticas.
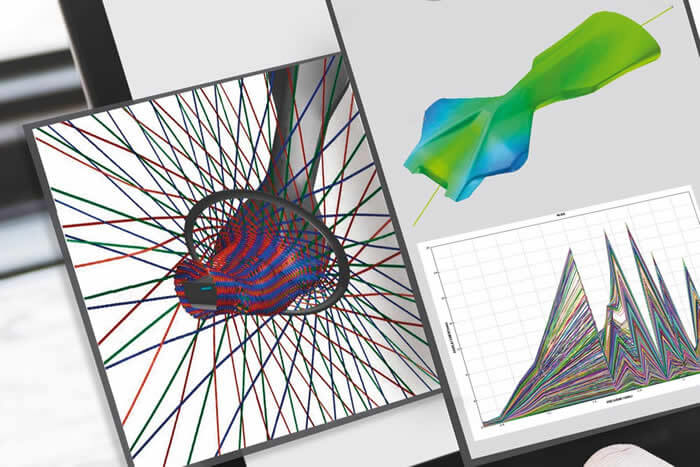
Um componente central da tecnologia CAVUS é o núcleo de areia da Reinsicht (anteriormente H2K Minerals). Para o Project R.A.C.E., o núcleo foi ajustado para uma resistência à temperatura de 330 °C e uma resistência à pressão de 500 bar. O núcleo demonstra suas características especiais mesmo após a infiltração da malha com a matriz. O desmoldagem do componente ocorre sem aumento do consumo de energia e somente com água. Além disso, a solução resultante não é tóxica. Por meio da separação independente dos componentes do núcleo, os componentes podem ser facilmente diferenciados e reciclados. Com isso, dependendo da combinação de materiais, é possível reutilizar até 98% do núcleo.
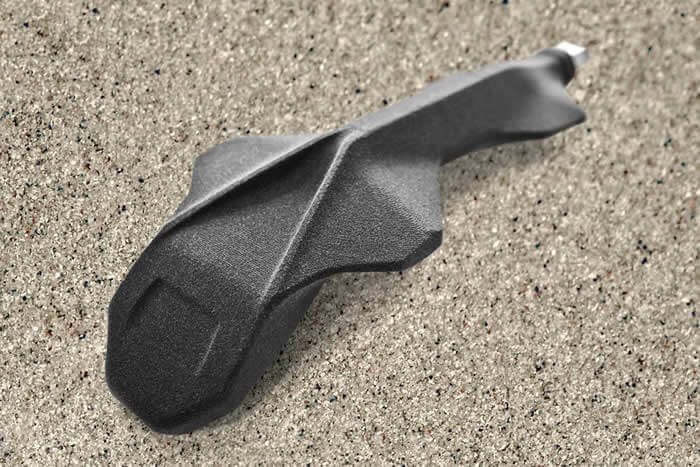
A aplicação das fibras foi implementada pelo Instituto para Construção Aeronáutica da Universidade de Stuttgart utilizando tecnologia de entrelaçamento. Para tanto, o núcleo foi fixado em um dispositivo de tensão no robô do sistema de entrelaçamento e guiado pela roda de entrelaçamento através do trajeto de entrelaçamento calculado na simulação. Para o Project R.A.C.E. foi utilizado um entrelaçador radial Herzog RF 1/64-100. Com 64 fios de entrelaçamento, consistindo de roquetes de fibra de carbono de 24k, o tecido foi aplicado ao núcleo. Quão fixamente a malha adere ao núcleo é determinado pela força das molas nas bobinas. 600 gramas de tração das molas proporcionaram o melhor resultado de flexibilidade e força para o trançado biaxial.
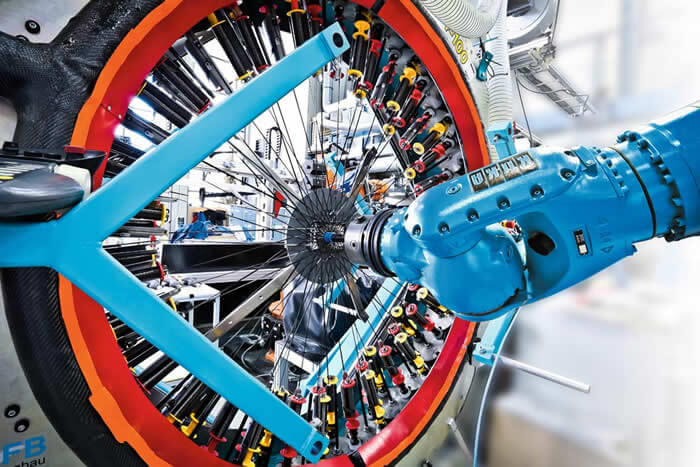
Propriedades mecânicas excepcionais, bem como uma excelente capacidade de processamento caracterizam o sistema de poliuretano VITROX® RTM 332 da empresa Huntsman, utilizado para o suporte de placa de licença da Superduke 1290R. A alta resistência ao impacto e a maleabilidade do material atendem aos requisitos do componente. Especialmente importante para o processo HP-RTM são as propriedades de processamento, já que o tempo de ciclo conta em uma produção em série. Com um tempo ajustável de “snap-cure” (cura instantânea) que varia de 30 segundos a 24 horas, até mesmo os tempos de ciclo mais curtos podem ser realizados com o VITROX®.
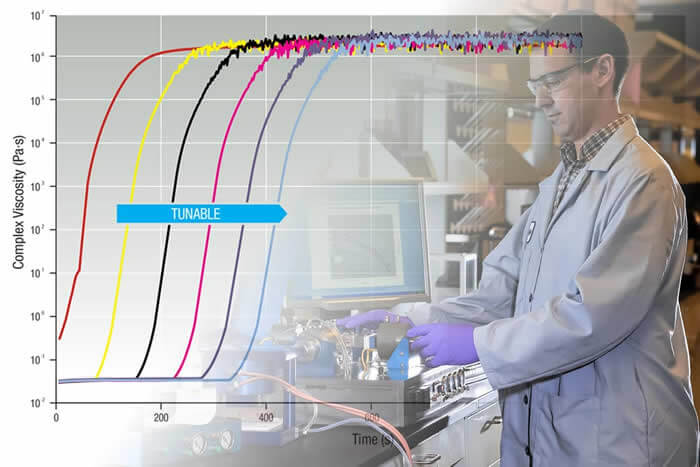
Especialmente a alta e constante qualidade do componente é um argumento decisivo para o uso do processo HP-RTM. No Project R.A.C.E. a configuração da instalação é composta por uma máquina dosadora Hennecke do tipo STREAMLINE e uma prensa de fechamento vertical do tipo Engel elast 400V compact. Graças à cooperação intensiva das empresas Engel e Hennecke, todo o processo pode ser controlado através de uma instalação. Os dois componentes poliol e isocianato são processados no sistema de dosagem STREAMLINE. Devido ao controle de temperatura de todo o sistema, incluindo os pacotes de mangueiras, uma temperatura constante é assegurada pela recirculação dos componentes. Além disso, um agente separador homogeneizado pode ser injetado através de um terceiro feixe.
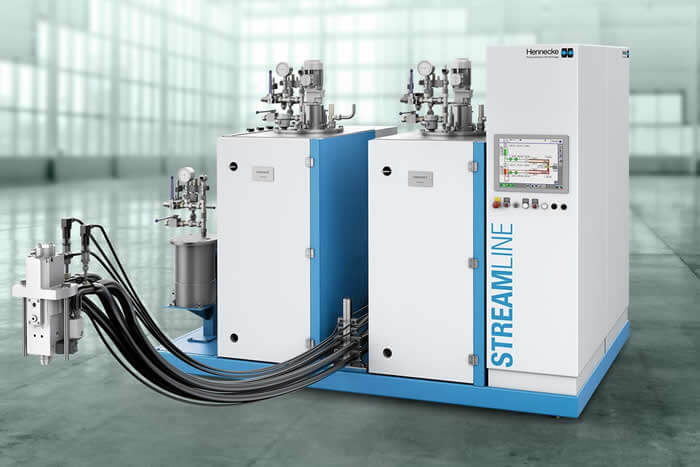
Para a mistura dos componentes, a Hennecke utiliza seu recentemente desenvolvido cabeçote de mistura MN10-3 RTM. O tubo de saída cônico com sensor de pressão de cavidade integrado permite que o cabeçote de mistura de alta pressão seja usado para operações de ancoragem semi-automáticas. A fim de impedir o encolhimento da polimerização, o tucho autolimpante também proporciona a função de pressão hidraulicamente controlada durante a cura da matriz. Desse modo, é possível obter superfícies da mais alta qualidade. Outra característica especial do MN10-3 RTM é o equipamento de série com injetores de pressão constante patenteados. Como resultado, uma possível influência da pressão de cavidade do molde sobre a distribuição de pressão dos componentes é completamente evitada.
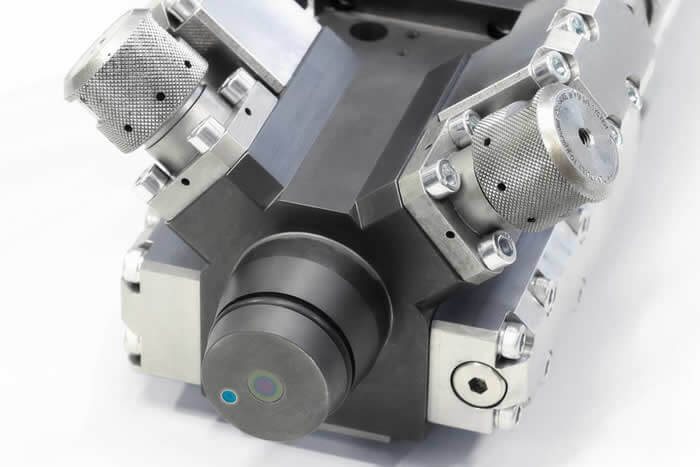
A utilização de plásticos altamente reativos com pressões de cavidade de até 200 bar demanda um alto desempenho da tecnologia de ferramentas. Por um lado, a ferramenta tem que oferecer uma longa vida útil na utilização de fibras abrasivas de carbono; por outro lado, devem garantir uma superfície uniforme e altamente polida. Graças ao know-how do fabricante de ferramentas Persico de Nembro, na Itália, foi possível que esses requisitos fossem implementados com sucesso no Project R.A.C.E. Com pressões médias de cavidade de aproximadamente 100 bar, a vedação também deve atender aos altos requisitos. Para isso, foi utilizado um novo tipo de material de vedação da empresa Murtfeldt. Murloc®, um material sintético termoplástico, oferece o mais alto desempenho de vedação em várias centenas de ciclos de processo. Em comparação com os cordões redondos convencionais, o material vedante é resistente a danos causados por materiais residuais ou fibras de carbono e também é quimicamente inerte a sistemas de resina reativa.
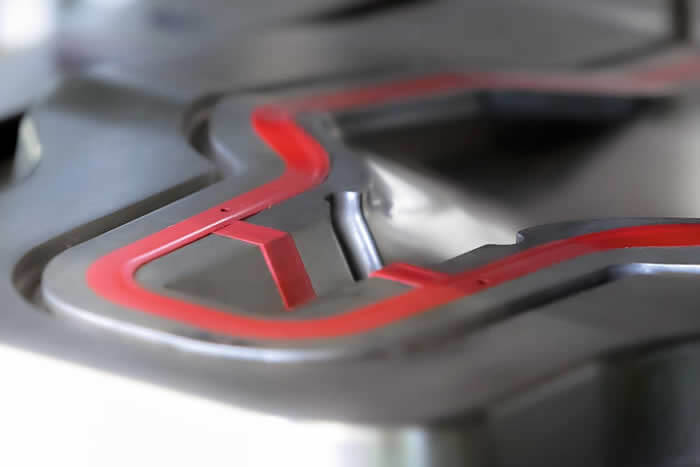
A desmoldagem do material do núcleo com o uso de água é uma característica exclusiva da tecnologia CAVUS. O que também torna essa tecnologia especial é o fato da sustentabilidade estar em primeiro plano. O núcleo pode ser liberado do componente sem o uso de solventes adicionais, prejudiciais ao meio ambiente. Depois de separar o componente desmoldado das bordas de corte, ele é colocado em um banho de água. A areia se decanta na solução e, após a secagem, pode ser completamente reutilizada para novos núcleos. O aglutinante que se encontra na solução pode ser descartado como água de processo ou mesmo usado como fertilizante para a agricultura. Depois de liberada a areia, o componente pode ser fornecido para as etapas usuais de pós-processamento de componentes compósitos de fibra e, em última instância, instalado no veículo.
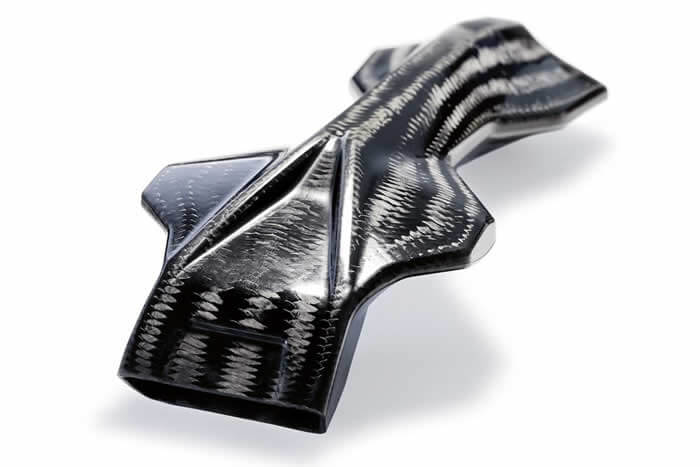
Declarações do parceiro de projeto
Produção ao vivo do componente durante a feira K-Messe em Düsseldorf
Cerca de 4.000 visitantes visitaram o stand da Hennecke para ver o processo. Um tempo de ciclo de parte a parte de 125 segundos e uma redução de peso de mais de 62 por cento, com uma valorização simultânea do produto, são ótimos argumentos para um projeto bem-sucedido. Com isso, o Project R.A.C.E. demonstra de forma impressionante como os esforços conjuntos de parceiros de projetos altamente especializados podem levar a um passo de desenvolvimento decisivo na produção em série de componentes ocos de compósitos de fibra baseados na tecnologia CAVUS.
PROJECT R.A.C.E. “2.0”
Suportes de placa de licença em construção híbrida (GFRP/CFRP)
O Project R.A.C.E. está em constante evolução. A mais recente abordagem de produção é um suporte de placa de licença na construção híbrida, o que garante um máximo em termos de liberdade de design e de coloração. Aqui, o contorno no processo de entrelaçamento é realizado com fibras de vidro. Através de um reforço preciso e orientado para cargas, usando fibras de carbono no processo TFP (Tailored Fiber Placement), o usuário obtém um componente que alcança valores de rigidez máximos com peso mínimo e custos significativamente reduzidos de matéria-prima. Além disso, uma vedação de núcleo melhorada reduz o número de etapas de processo necessárias, o que também minimiza os custos de produção. Adicionalmente, a nova abordagem de produção também permite a integração fácil de componentes eletrônicos, tais como sensores ou LEDs.
Clique aqui para documentos de acompanhamento em formato PDF
Para visualizar os documentos PDF, você precisará do Adobe Reader®, que pode ser baixado gratuitamente aqui.