Bulk chemical storage and blending systems
Hennecke storage and blending solutions are available in a range of types, sizes and modular configurations. Our design engineers work with customers to determine the best combination of storage and blending equipment to satisfy their unique chemical and production requirements.
Bulk chemical storage systems unload, store and transfer intermediate to large quantities of raw materials within a closed loop, minimizing opportunities for contamination, spills, evaporation and employee or environmental exposure.
Blending systems allow in-house formulation of liquid or liquid and solid particle blends to achieve the specific characteristics of an end product. Polyols typically require the addition of blowing agents, activators, emulsifiers, foam stabilizers, flame retardants or other auxiliary materials to achieve those characteristics.
Bulk storage systems for larger volumes of chemicals include unloading stations for materials delivered by tanker truck or rail car, storage tanks, transfer pumps and all required controls, valves, instrumentation, safety devices and piping.
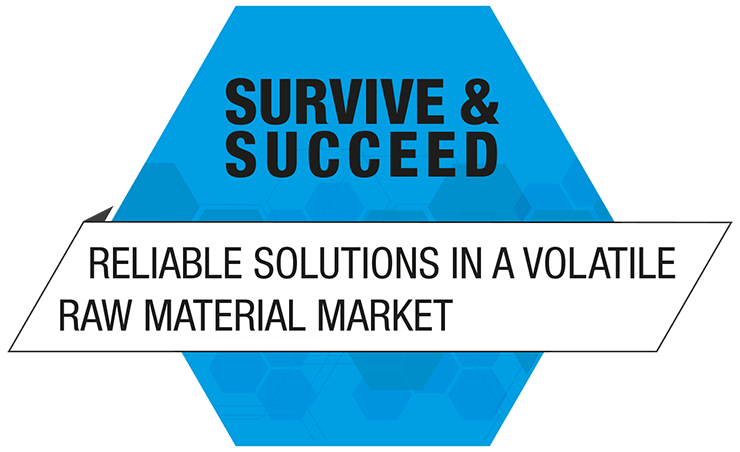
It has been known for years that companies with extensive chemical exposure have to constantly manage raw materials volatility. It is essential for not only short-term growth but also long-term competitive advantage. If unsuccessful, companies run into difficulties fast or even find themselves struggling to survive. For well over 50 years, Hennecke has been supplying and educating customers of the advantages of Bulk Chemical Storage and Blending Systems. Even under the best of circumstances, raw materials present an almost constant concern and quite frankly, headache, for manufacturers. When combining the positive impact of the increase in global demand with many other unpredictable and unforeseen negative factors, the end result is exactly our current situation: chemical shortages and extreme price hikes. Unfortunately, this will happen time and time again.
Will you take the necessary measures to protect yourself in the future by minimizing disruptions to your supply and mitigating price increases all while optimizing your internal processes and efficiencies? Hennecke is able to offer you a tailor-made storage and blending solution that meets your specific needs. In addition to the many other benefits, you will effectively avoid such consequences during the next crisis!
Raw material storage systems sized to customer needs
Stable storage and handling of polyol, isocyanate, blowing agents and additives ultimately lead to higher quality products. Hennecke’s state-of-the-art equipment and technology for intermediate and bulk storage solutions are designed to maintain raw materials at the optimum processing condition.
Bulk unload stations with pump or pressure transfer
Bulk unload stations are designed for safe, efficient unloading of liquid raw materials delivered by tanker truck or rail car.
The delivery tanker begins unloading chemicals by connecting to pipe couplings and valves mounted in an unload station box. For high viscosity chemicals or longer distances, unload pumps move the chemical from delivery tanker to the bulk storage tank. For short distances and low viscosity materials, a pressure transfer method may be used. A blanket of dry air or nitrogen pressurizes the delivery tanker to push the chemical from tanker to the bulk storage tank.
Transfer pumps and temperature control
Chemicals used in polyurethane processing are sensitive to temperature and flow fluctuations. Pumps, equipped with variable speed drives, are selected for the type and viscosity of chemical being transferred from storage tanks to blending or metering systems. Tempering devices, such as heat exchangers, temperature control units and chillers, in a closed cooling system ensure appropriate conditioning of primary components.
Blending systems for liquids and powders
Blending systems precisely meter and blend various additive into the main polyol stream to improve both mixing ability and reaction behavior. Hennecke offers proven equipment for conditioning, blending and mixing raw materials with the polyol stream, including static or dynamic mixers and integrated gas loading units.
Specialized bulk systems for flammable materials
Hennecke experts have the know-how for safe processing of the eco-friendly blowing agent pentane. Because pentane can create an explosive atmosphere at certain gas concentrations our Pentane Process Technology (PPT) comprises a catalogue of primary and secondary safety measures to prevent emergence of explosive mixes right from the start. Our years of global experience with these systems means we can offer you a suitable concept that complies with national and international directives as well as local regulations and requirements.
Within the Hennecke GROUP, the bulk storage systems are exclusively manufactured and distributed by Hennecke Inc. with its head office in Pittsburgh (USA).
Click here for accompanying documents in the PDF format
You will need Adobe® Reader® that you can download here for free.